
Area Vasta Emilia Nord (AVEN) is a consortium of six healthcare organizations operating across the Emilia Romagna region, covering the provinces of Piacenza, Parma, Reggio Emilia, and Modena.

5800
hospital beds

90
nursing homes

2 University
hospital groups

660M €/yrs
annual turnover
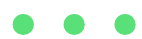
Since 2022, it has chosen

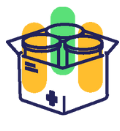
A Centralized
Warehouse
with the most advanced logistics standards
Artificial Intelligence
to Optimize Procurement and Distribution
The main goal is to streamline medicine distribution across all facilities, virtually eliminating stockouts (product shortages) caused by inefficient restocking.
The project relies on five years’ worth of data from AVEN-affiliated facilities, which has been collected and standardized.
the BENEFITS
The true value of this project extends beyond just solving stockout issues,
AI algorithms are also helping to optimize stock levels in the warehouse.
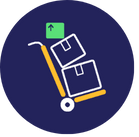
AVERAGE STOCK
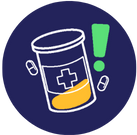
STOCKOUTS
and the prevention of unscheduled orders
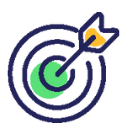
By using a “double-blind” comparison between the traditional order system and the AI-powered model, results from the first few months—focused on 84 products—show a potential 17% reduction in average stock levels, a 12% decrease in stockouts, and the elimination of unplanned orders.
As a result, the project offers potential improvements in service quality, cost reductions, faster inventory turnover, and more efficient space management in the long term.
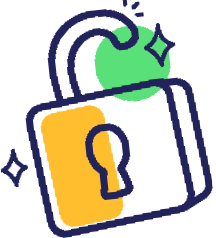